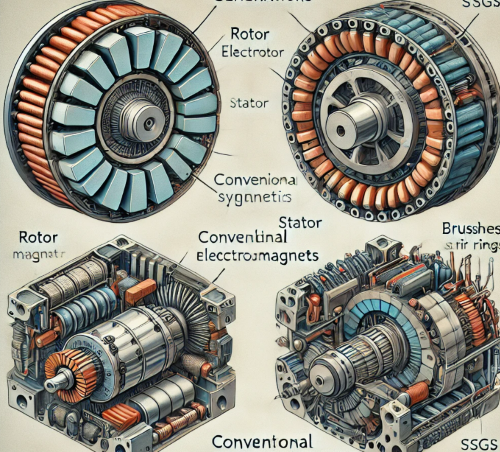
Introduction
In the quest for efficient and reliable energy generation, the comparison between Permanent Magnet Generators (PMGs) and Conventional Synchronous Generators (CSGs) becomes increasingly relevant. Both technologies play pivotal roles in various applications, but their differences in design, efficiency, performance, and maintenance highlight distinct advantages and limitations. This article delves into these aspects to provide a comprehensive understanding of each generator type.
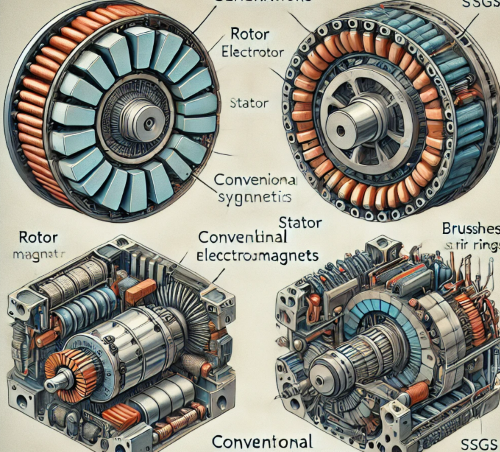
1. Principles of Operation
Permanent Magnet Generators (PMGs) operate on the principle of electromagnetic induction, where permanent magnets create a magnetic field that induces an electric current in the stator windings. This eliminates the need for an external power source for excitation, resulting in a simpler and more robust design. The magnets used in PMGs, often rare earth magnets like neodymium, provide a strong and consistent magnetic field.
Conventional Synchronous Generators (CSGs), on the other hand, require an external DC power source to excite the rotor windings, creating the necessary magnetic field. This excitation can be provided by an external excitation system or through the use of an exciter machine mounted on the same shaft. The generated magnetic field interacts with the stator windings to produce electricity.
Related reading: Permanent Magnet Generator: An Overview
2. Design and Construction
PMGs feature a rotor embedded with permanent magnets and a stationary stator with windings. The lack of brushes and slip rings simplifies the construction, reduces friction losses, and minimizes maintenance requirements. The use of high-performance materials like rare earth magnets, however, can drive up the initial cost.
CSGs consist of a rotor with electromagnets and a stator with windings. The electromagnets are powered by an external DC source, necessitating the use of brushes and slip rings to transmit power to the rotor. This design is well-established and versatile, making CSGs a common choice in large-scale power plants and industrial applications.
3. Efficiency and Performance
Efficiency is a critical metric in evaluating generators. PMGs typically exhibit higher efficiency due to the absence of excitation losses. The direct generation of the magnetic field by permanent magnets results in lower energy consumption and higher overall efficiency. However, PMGs can suffer from magnetic losses, especially at high speeds.
Performance Metrics such as power output, torque, and speed characteristics differ significantly between the two types. PMGs deliver consistent performance across a range of speeds, making them ideal for variable-speed applications like wind turbines. CSGs, while effective at maintaining synchronization with the grid, can experience efficiency drops at lower speeds due to higher excitation losses.
4. Material Requirements
The reliance on rare earth materials for PMGs poses both an advantage and a challenge. These materials provide strong magnetic fields but are costly and subject to supply chain vulnerabilities. The increasing demand for rare earth elements in various industries can also impact the availability and price stability of these materials.
CSGs use more readily available materials, such as copper for windings and iron for the core, which are generally easier to source and less expensive. The use of electromagnets allows for more flexibility in design and scalability for large-scale applications.
5. Maintenance and Reliability
PMGs are lauded for their low maintenance requirements. The absence of brushes and slip rings eliminates common wear points, reducing the need for regular maintenance and increasing the generator’s lifespan. This makes PMGs particularly appealing for remote or inaccessible locations where maintenance can be challenging.
In contrast, CSGs require regular maintenance to ensure the brushes and slip rings are in good condition. These components are prone to wear and can lead to increased downtime and operational costs. However, the familiarity and established maintenance protocols for CSGs can mitigate some of these concerns.
6. Applications
PMGs are widely used in renewable energy applications, such as wind turbines and small-scale hydroelectric systems. Their ability to operate efficiently at varying speeds makes them ideal for these environments. Additionally, PMGs are popular in portable generators and off-grid power systems due to their reliability and low maintenance needs.
CSGs are prevalent in large-scale power generation facilities, including thermal, hydroelectric, and nuclear power plants. Their ability to maintain synchronization with the grid and handle high power outputs makes them suitable for these demanding applications. CSGs are also used in industrial settings where consistent and reliable power is essential.
Related reading: Types and Uses of Permanent Magnet
Advantages and Limitations
PMGs offer higher efficiency, lower maintenance, and a more compact design compared to CSGs. However, their higher initial cost and reliance on rare earth materials can be significant drawbacks. CSGs, while less efficient and requiring more maintenance, benefit from lower initial costs, easier material sourcing, and proven reliability in large-scale applications.
Conclusion
The choice between Permanent Magnet Generators and Conventional Synchronous Generators depends largely on the specific requirements of the application. PMGs are well-suited for renewable energy and situations where low maintenance is crucial, while CSGs remain a robust choice for large-scale power generation and industrial uses. Understanding the strengths and limitations of each technology can guide decision-makers in selecting the most appropriate generator type for their needs. For more information, please check Stanford Magnets.