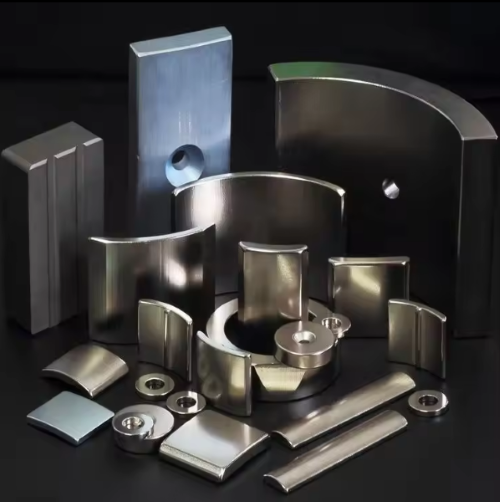
Introduction
Neodymium magnets are renowned for their exceptional magnetic strength, making them a popular choice across a wide range of industries. However, their performance can suffer when exposed to high moisture, corrosive chemicals, or extreme temperatures. To overcome these challenges, PTFE (Polytetrafluoroethylene) coatings are applied to neodymium magnets, significantly enhancing their durability and expanding their range of applications. This article will talk about their key characteristics, applications, and specific case studies.
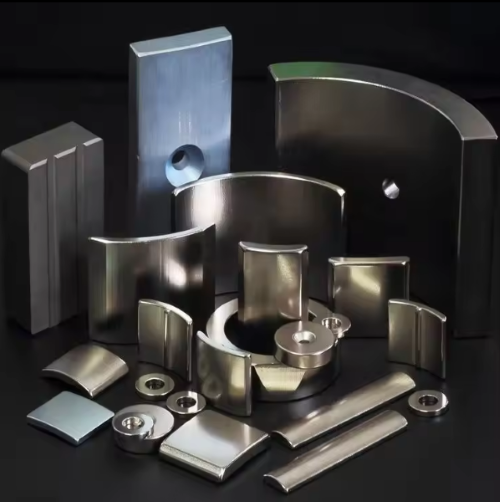
Types of Neodymium Magnet Coatings
Neodymium magnets are often coated to improve their resistance to environmental factors. Various coatings are available, each offering specific benefits:
- Nickel (Ni): The most common magnet coating, providing good corrosion resistance and a smooth finish. It’s a cost-effective option for general applications.
- Zinc (Zn): Offers a matte finish and decent corrosion protection. These magnet coatings are used in applications where aesthetics are less critical.
- Epoxy: Provides excellent corrosion resistance and is often used in humid environments. However, it can be prone to chipping.
- Gold (Au): Offers excellent corrosion resistance and biocompatibility, making it suitable for medical applications.
- PTFE (Polytetrafluoroethylene): Provides superior corrosion resistance, low friction, and excellent temperature stability, making it ideal for demanding environments.
Related reading: Types of Neodymium Magnet Coatings: Protecting the World’s Strongest Magnets
Key Characteristics of PTFE Coated Neodymium Magnets
Let’s continue by discussing PTFE coatings. PTFE-coated neodymium magnets stand out due to several key characteristics:
1. Superior Corrosion Resistance:
PTFE coating provides an excellent barrier against corrosive agents. In an ASTM B117 salt spray test, PTFE-coated neodymium magnets maintained their integrity after 200 hours of exposure, showing no significant signs of corrosion. In contrast, uncoated magnets often show rust within 48 hours.
2. Low Friction Surface:
The PTFE coating has a low friction coefficient, typically between 0.05 and 0.20. This property reduces wear and tear on the magnets and associated components, making PTFE-coated neodymium magnets ideal for sliding or moving applications.
3. Temperature Stability:
PTFE-coated neodymium magnets can operate effectively in temperatures ranging from -200°C to +260°C. Unlike standard neodymium magnets, which lose their magnetic properties above 150°C, PTFE-coated magnets maintain their performance in extreme temperatures.
4. Chemical Resistance:
PTFE is chemically inert, allowing PTFE-coated neodymium magnets to withstand exposure to acids, bases, and other corrosive chemicals without degrading, making them suitable for use in chemical processing environments.
5. Electrical Insulation:
PTFE coating is an excellent electrical insulator, with a dielectric strength of up to 60 kV/mm. This makes PTFE-coated magnets safer for use in electronic and electrical applications, preventing short circuits and improving overall safety.
Applications of PTFE Coated Neodymium Magnets
Thanks to their enhanced properties, PTFE-coated neodymium magnets are used in a wide range of applications:
1. Marine Environments:
In marine applications, magnets are often exposed to saltwater, which can cause rapid corrosion. PTFE-coated magnets are ideal for use in navigation systems, underwater propulsion units, and other marine equipment due to their resistance to saltwater and corrosion.
2. Chemical and Pharmaceutical Industries:
These PTFE-coated neodymium magnets are perfect for use in chemical processing and pharmaceutical manufacturing, where they may come into contact with aggressive chemicals. PTFE coating ensures that the magnets maintain their performance without degrading.
3. Medical Devices:
In medical applications, magnets must be biocompatible and resistant to biofluids. PTFE-coated magnets are used in MRI machines, implantable devices, and other medical equipment, offering both magnetic strength and resistance to corrosion from bodily fluids.
4. Automotive Industry:
PTFE-coated magnets are used in electric motors, sensors, and other automotive components that are exposed to harsh conditions such as high temperatures and chemicals. The coating improves the durability and reliability of these critical components.
5. Food Processing:
In the food industry, PTFE-coated magnets are used for detecting and separating metal contaminants. The coating not only protects the magnet from corrosion but also ensures that the magnets remain clean and functional during repeated washdowns.
Case Study of PTFE Coated Neodymium Magnets
–Challenge
Imerys, one of the largest graphite and carbon companies, faced significant challenges with the magnets used in their industrial production equipment, such as electromagnetic filters, liquid pipeline separators, and metal detectors. These neodymium (NdFeB) magnets were exposed to highly corrosive environments and high temperatures, leading to rapid corrosion and frequent loss of magnetism.
The company attempted to mitigate these issues by using epoxy and plastic coatings, but these materials proved inadequate due to their poor heat resistance and aging properties. As a result, Imerys had to frequently replace the magnets, which not only disrupted production but also incurred substantial costs.
–Solution
Stanford Magnets, leveraging their extensive experience in magnet manufacturing, proposed a more effective solution: PTFE (Teflon) coated neodymium magnets.
PTFE is known for its excellent resistance to acids and most corrosive chemicals, as well as its ability to remain flexible at low temperatures and stable at high temperatures. These properties made PTFE an ideal coating material for the challenging conditions in Imerys’ production processes. The PTFE coating provided a durable barrier that protected the neodymium magnets from the harsh environment, preventing corrosion and maintaining their magnetic strength.
–Results
The implementation of PTFE-coated magnets successfully addressed the challenges faced by Imerys. Although the PTFE-coated neodymium magnets were initially more expensive—costing twice as much as the uncoated magnets—the overall expenses were reduced by 50%. This cost reduction was achieved by eliminating the need for frequent magnet replacements and reducing the frequency of machine maintenance and checks.
The solution not only improved production efficiency but also provided significant economic benefits, making the work of frontline production staff easier and more efficient. This case underscores Stanford Magnets‘ ability to deliver specialized and effective solutions for demanding industrial applications.
Conclusion
PTFE-coated neodymium magnets come with superior corrosion resistance, low friction, temperature stability, and chemical resistance, making them a preferred choice for marine, chemical, medical, automotive, and food processing. As technology continues to advance, the use of PTFE-coated neodymium magnets is likely to expand, providing innovative solutions for increasingly complex industrial challenges.