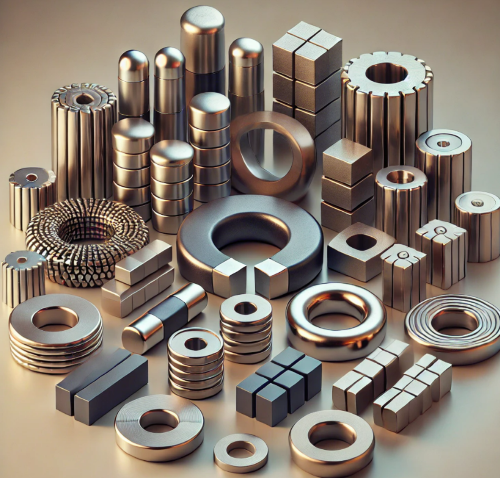
Introduction
Whether it’s in the devices we use daily or the industrial systems that keep society moving, permanent magnets create a consistent magnetic field without any external power. What’s even more fascinating is that there are several different types of permanent magnets, each with its own strengths and limitations.
In this article, we’ll discuss four main types of permanent magnets—Ferrite, Alnico, Neodymium, and Samarium-Cobalt—and how they contribute to the technologies shaping our world.
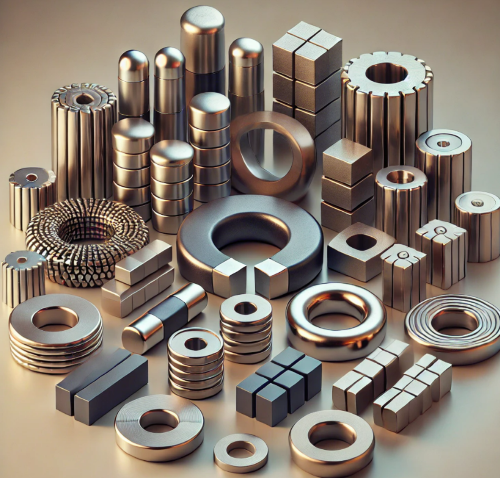
1. Ferrite Magnets: Affordable Power for Everyday Use
Ferrite magnets, also called ceramic magnets, are made from iron oxide combined with barium or strontium carbonate. These magnets are popular because of their low cost and their ability to resist corrosion without any special coatings.
They also perform well in high-temperature environments, maintaining stability at temperatures up to 250°C. However, their magnetic strength is moderate, which limits their use in high-performance scenarios.
Where You’ll Find Them:
– Holding photos on your refrigerator
– Creating sound in loudspeakers
– Powering small DC motors in toys and appliances
– Detecting motion in sensors
2. Alnico Magnets: High-Temperature Performers
Alnico magnets, made from a blend of aluminum, nickel, and cobalt, were once the strongest magnets available before the advent of rare-earth magnets. They are still widely used today in applications where resistance to high temperatures is crucial.
Alnico magnets can withstand extreme temperatures, maintaining their magnetic properties even at temperatures over 500°C. However, they have relatively low coercivity, meaning they are more easily demagnetized compared to other magnets. While they offer moderate magnetic strength, their high-temperature tolerance keeps them in demand for specific applications.
Common Uses:
– Enhancing the sound in electric guitar pickups
– Providing precision in sensors and scientific instruments
– Powering motors in industrial machinery
– Generating electricity in specific types of generators
3. Neodymium Magnets: The Strongest of Them All
Neodymium magnets, also known as NdFeB magnets, are part of the rare-earth family and hold the title of the strongest permanent magnets available today. These magnets are made from an alloy of neodymium, iron, and boron, and their sheer power has revolutionized industries that rely on compact, high-performance magnets.
Neodymium magnets pack incredible magnetic strength, allowing them to be used in smaller, more efficient designs without sacrificing power. Despite their strength, they are fragile and prone to corrosion, so they require protective coatings like nickel or zinc. Another challenge is their temperature sensitivity; they begin to lose magnetic strength at temperatures above 80°C, though some specialized grades can withstand higher heat.
Where Neodymium Magnets Shine:
– Driving electric motors in vehicles
– Generating power in wind turbines
– Storing data in hard disk drives
– Creating secure closures in magnetic fasteners
– Powering medical imaging devices like MRI machines
4. Sm-Co Magnets: Strength Meets Temperature Stability
Samarium-cobalt magnets are another type of rare-earth magnet, known for their excellent performance in high-temperature and corrosive environments. These magnets are a go-to option for industries where both strength and durability are critical.
These magnets offer impressive temperature stability, maintaining their magnetic properties at temperatures as high as 350°C. Unlike neodymium magnets, they are highly resistant to corrosion and do not require protective coatings. Although they are not as strong as neodymium magnets, they strike a balance between magnetic strength and environmental resilience.
Applications That Rely on Samarium-Cobalt Magnets:
– Propelling aerospace and defense systems
– Powering high-performance motors in industrial settings
– Driving magnetic couplings in harsh environments
– Enhancing the reliability of oil and gas exploration tools
Comparison of Specific Properties
When choosing the right permanent magnet for an application, understanding the key properties of each type is essential. Here is a detailed comparison of Ferrite, Alnico, Neodymium, and Samarium-Cobalt magnets, including magnetic strength, operating temperature, coercivity, and cost.
Property | Ferrite | Alnico | NdFeB | SmCo |
Magnetic Strength (BHmax) | 3-4 MGOe | 5-9 MGOe | 33-52 MGOe | 16-32 MGOe |
Coercivity (Hc) | 2.3-2.5 kOe | 0.5-1.0 kOe | 10-12 kOe | 9-10 kOe |
Curie Temperature | 450°C | 860°C | 310°C | 750°C |
Max Operating Temperature | 250°C | 525°C | 80-200°C | 250-350°C |
Corrosion Resistance | Excellent (no coating needed) | Fair (can oxidize, needs coating) | Poor (requires coating) | Excellent (no coating needed) |
Cost | Low | Moderate | High | Very High |
Temperature Coefficient of Br | -0.19%/°C | -0.02%/°C | -0.12%/°C | -0.04%/°C |
Durability | Brittle, corrosion -resistant | Tough But easily demagnetized | Brittle and needs coating | Tough, excellent resistance |
Stanford Magnets specializes in manufacturing and supplying premium permanent magnets and magnetic products. We offer a wide range of options, including neodymium magnets (NdFeB), samarium cobalt magnets (SmCo), alnico magnets, ceramic magnets, and magnetic assemblies. Hope that you can find the ideal magnetic solution.
Conclusion
Each type of permanent magnet has specific strengths and limitations. Ferrite magnets are inexpensive and corrosion-resistant but weaker. Alnico magnets are durable in high-heat environments but prone to demagnetization. Neodymium magnets, the most powerful, excel in performance but require protective coatings and careful temperature management. Samarium-cobalt magnets strike a balance between strength, temperature stability, and corrosion resistance, making them a versatile choice for demanding applications.