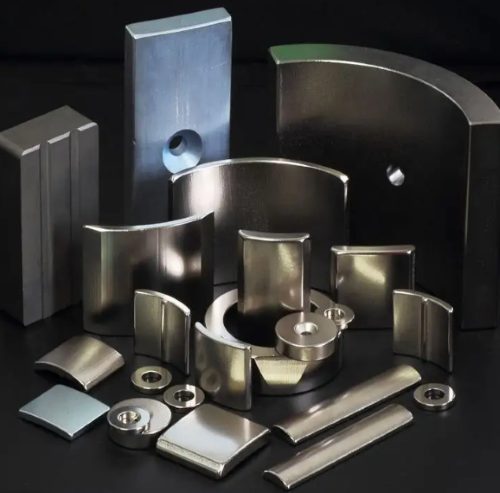
Introduction
Magnets play a critical role in modern technology. Among the various types of magnets available, Alnico and Neodymium magnets stand out due to their distinctive properties and broad applications. Although both types are widely used, their magnetic characteristics, performance in different environments, and best-suited applications differ significantly. Let’s explore the key differences in this article.
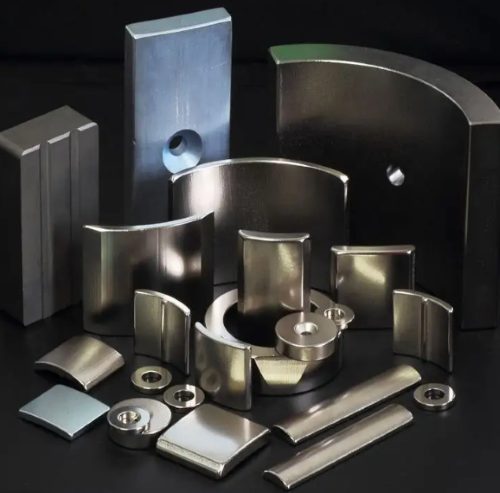
1. Composition and Manufacturing
- Alnico magnets are composed primarily of aluminum (Al), nickel (Ni), cobalt (Co), and iron (Fe), often with additional elements like copper or titanium. They are either cast or sintered to form different shapes. Cast Alnico magnets tend to have better magnetic properties, while sintered Alnico magnets offer finer dimensional control.
- Neodymium magnets are made from a combination of neodymium (Nd), iron (Fe), and boron (B), forming what is known as the NdFeB alloy. They are produced through a powder metallurgy process that involves pressing and sintering fine particles of this alloy. Neodymium magnets belong to the family of rare earth magnets, known for their exceptionally high magnetic strength.
2. Magnetic Strength
- Alnico magnets are considered medium-strength magnets. Their magnetic strength is considerably lower compared to Neodymium magnets, with a maximum energy product (BHmax) ranging from 1 to 5 megagauss-oersteds (MGOe). Although not the strongest, Alnico magnets maintain a stable magnetic field over time and are suitable for applications where moderate strength is sufficient.
- Neodymium magnets are the strongest commercially available magnets, with a maximum energy product (BHmax) of 30 to 52 MGOe, making them significantly more powerful than Alnico magnets. Their incredible strength allows for smaller magnets to achieve the same performance as larger Alnico magnets, which is advantageous in miniaturized devices or applications where space is limited.
3. Temperature Stability
- One of the key advantages of Alnico magnets is their excellent temperature stability. They can withstand operating temperatures as high as 540°C (1000°F) without losing significant magnetism. This makes them ideal for high-temperature environments, such as in aerospace, industrial furnaces, or military applications.
- While Neodymium magnets offer higher magnetic strength, they are more sensitive to high temperatures. Standard Neodymium magnets begin to lose magnetic strength at around 80°C (176°F), though high-temperature grades can operate up to 200°C (392°F). This limitation makes Neodymium less suitable for use in high-temperature environments compared to Alnico magnets.
Related reading: List of Magnets That Can Withstand High Temperatures
4. Resistance to Demagnetization
- Alnico magnets have a low coercivity, meaning they are more prone to demagnetization by external magnetic fields. This low resistance to demagnetization makes them less ideal for applications where they might be exposed to opposing magnetic forces. However, Alnico’s magnetic field is stable over time if the environment remains consistent.
- Neodymium magnets possess high coercivity, making them highly resistant to demagnetization even when exposed to strong external magnetic fields. This property makes Neodymium magnets more durable and suitable for applications where exposure to other magnetic fields or mechanical shock might be an issue.
5. Corrosion Resistance
- Alnico magnets are highly resistant to corrosion and oxidation, making them suitable for outdoor or harsh environments. They do not require additional coatings, unlike Neodymium magnets.
- Neodymium magnets are susceptible to corrosion, particularly in moist environments. To counteract this, they are usually coated with protective layers such as nickel, zinc, or epoxy to prevent rusting. The need for coatings can increase costs and impact the lifespan of Neodymium magnets in corrosive conditions.
6. Cost and Availability
- Although Alnico magnets have been widely used for decades, their production costs are relatively high due to the inclusion of cobalt and nickel, which are more expensive materials. However, they remain widely available and cost-effective for applications that do not require extreme magnetic strength.
- Despite being much more powerful, Neodymium magnets are cheaper on a per-unit basis than Alnico magnets for the same magnetic strength. However, the total cost can rise when factoring in protective coatings and custom shapes. Their widespread availability makes them a popular choice in consumer electronics, motors, and renewable energy technologies.
7. Common Applications
Due to their temperature stability and resistance to corrosion, Alnico magnets are commonly used in high-temperature applications. Key industries include:
– Musical instruments (e.g., guitar pickups and microphones)
– Sensors and measuring devices
– High-temperature industrial equipment
– Scientific instruments (e.g., magnetometers)
Neodymium magnets, given their exceptional strength, are widely used in applications that demand compact size and high magnetic force. Common uses include:
– Consumer electronics (e.g., headphones, smartphones, hard drives)
– Electric motors and generators
– Magnetic fasteners and closures
– Medical devices (e.g., MRI machines and surgical tools)
– Renewable energy (e.g., wind turbine generators)
Conclusion
Alnico and Neodymium magnets each have unique magnetic properties that make them suitable for different applications. Alnico magnets offer excellent temperature stability and resistance to corrosion. However, their lower magnetic strength and susceptibility to demagnetization may limit their use in certain modern applications. Neodymium magnets boast the strongest magnetic field, though they require additional care in high-temperature and corrosive conditions. For more information, please check Stanford Magnets.