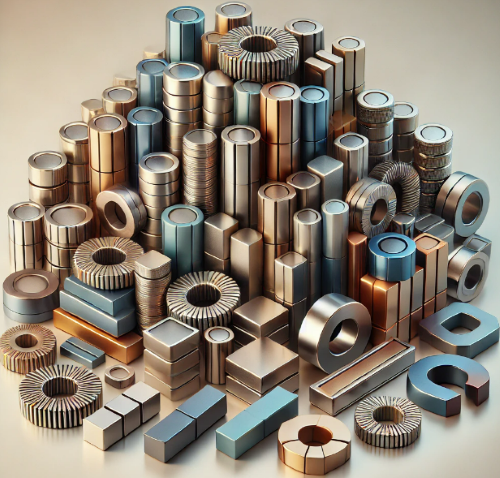
Introduction
Rare earth magnets, known for their exceptional strength, are popular in many applications. However, like many materials, rare earth magnets are not immune to environmental factors, especially moisture, which can lead to rust or corrosion. This article explores the corrosion susceptibility of rare earth magnets and the protective measures used to ensure their durability.
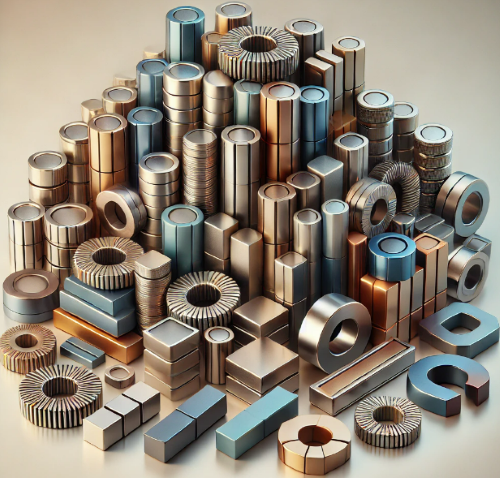
Why Do Magnets Rust?
Rust is a form of corrosion that primarily affects iron and iron-based alloys when they’re exposed to oxygen and moisture. The process creates iron oxide, a reddish-brown flaky substance that weakens the material’s structural integrity. Since rare earth magnets are typically made with iron-containing alloys, they can be prone to corrosion, especially neodymium magnets, which are more vulnerable than samarium cobalt magnets.
Corrosion in Rare Earth Magnets
–Corrosion in Neodymium Magnets
Neodymium magnets, composed primarily of neodymium, iron, and boron (NdFeB), are the strongest and most widely used rare earth magnets. However, their high iron content makes them highly susceptible to rust and corrosion. When exposed to humid environments, unprotected neodymium magnets can start corroding quickly, leading to a breakdown of the magnet’s structure and a loss in magnetic strength. Corrosion causes neodymium magnets to become brittle, causing them to crack or break over time, making protective measures essential.
–Protective Coatings for Neodymium Magnets
To prevent rust, most neodymium magnets are coated with a protective layer. Here are some common coating options:
- Nickel-Copper-Nickel (Ni-Cu-Ni) Coating: The most common protective coating, Ni-Cu-Ni consists of a nickel layer, followed by a copper layer, and finished with another nickel layer. This triple coating provides good resistance to corrosion and is suitable for most general-purpose applications.
- Epoxy Coating: Epoxy coatings provide an additional layer of protection against moisture and are particularly useful for applications in damp or humid environments. However, epoxy can wear down over time, so it may not be suitable for long-term use in harsh conditions.
- Gold Coating: Some neodymium magnets are coated with gold for added corrosion resistance and a visually appealing finish. While effective, gold coatings are more expensive and are usually reserved for specific aesthetic or medical applications.
- PTFE (Teflon) Coating: PTFE-coated magnets offer high corrosion resistance and are often used in environments where chemicals or saltwater are present. This coating is common in medical and marine applications, where additional protection is essential.
Further reading: Something You Should Know About Neodymium Magnets Coatings
–Corrosion in Samarium Cobalt Magnets
Samarium cobalt (SmCo) magnets, made from samarium and cobalt, are the second most common rare earth magnets. They are slightly less powerful than neodymium magnets but have an advantage in terms of corrosion resistance. Unlike neodymium magnets, samarium cobalt magnets are much more stable in humid or high-temperature environments and are naturally resistant to rust and corrosion due to their cobalt content. This makes them ideal for demanding applications, such as aerospace or military uses, where exposure to extreme conditions is common.
Although SmCo magnets are more resistant to corrosion than NdFeB magnets, they are still coated in some applications to provide additional protection. However, coatings are generally less necessary for SmCo magnets, as their natural resistance makes them suitable for harsh environments without extra layers.
Factors That Influence Corrosion in Rare Earth Magnets
The risk of rusting in rare earth magnets depends on several factors:
1. Environment: Exposure to high humidity, saltwater, or acidic environments can accelerate corrosion. For instance, magnets used in outdoor, marine, or medical applications face a greater risk of rusting without protective coatings.
2. Temperature: Neodymium magnets are more vulnerable to high temperatures, which can weaken their magnetic strength and make them more susceptible to corrosion. SmCo magnets, on the other hand, perform well under extreme temperatures, reducing their risk of rusting.
3. Coating Quality: The effectiveness of a coating largely depends on its quality. Low-quality coatings can chip or wear away, allowing moisture to reach the magnet and cause rust. High-quality coatings, applied properly, provide long-lasting protection.
4. Application: For applications that require high durability, such as motors, medical devices, or outdoor equipment, coatings are crucial to prevent corrosion and ensure longevity.
How to Protect Rare Earth Magnets from Rusting
To maximize the lifespan of rare earth magnets, it’s essential to use proper protection methods. Here are some tips:
- Choose the Right Coating: Selecting the appropriate coating based on the application environment is crucial. For example, a Ni-Cu-Ni coating works well in most indoor applications, while a PTFE coating is better for marine or chemical exposure.
- Store in Dry Conditions: Storing magnets in a dry environment helps prevent rust. For neodymium magnets, in particular, it’s essential to avoid long-term exposure to moisture.
- Use SmCo Magnets in Extremely Harsh Environments: If your application involves extreme temperatures or a high risk of exposure to corrosive elements, samarium cobalt magnets are a better choice due to their natural corrosion resistance.
- Regular Inspection and Maintenance: For critical applications, inspect magnets periodically for signs of corrosion. Replacing magnets or adding protective measures can prevent larger failures.
Conclusion
Rare earth magnets, particularly neodymium magnets, can rust if they’re exposed to moisture or corrosive environments. Neodymium magnets are more prone to corrosion due to their iron content, but protective coatings like nickel, epoxy, gold, or PTFE provide a barrier against rust. Samarium cobalt magnets, on the other hand, have a natural resistance to rust, making them suitable for high-temperature and harsh applications without requiring extensive protection.
Choosing the right type of rare earth magnet and applying the appropriate protective measures are essential steps in ensuring the longevity and performance of these powerful magnets. Stanford Magnets specializes in manufacturing and supplying high-quality neodymium (NdFeB) magnets and various magnetic assemblies. Send us an inquiry if you are interested.